在
保安岗亭制作过程中,尺寸差异可能导致安装错位、外观不规整或功能受限等问题。避免尺寸偏差需从设计、材料加工、组装到质检全流程严格把控,以下是具体解决方案:
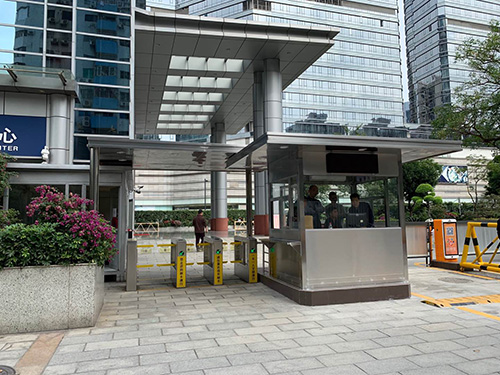
一、设计阶段:精准建模与图纸校验
1. 三维建模与尺寸标准化
使用 CAD 或 SolidWorks 等软件进行 1:1 三维建模,标注关键尺寸(长、宽、高、门窗位置、底板厚度等),公差控制在 ±2mm 内。
重点核对:
岗亭主体框架尺寸与运输通道、安装场地的匹配性(如门洞宽度需比岗亭宽度大 100-200mm)。
门窗尺寸与型材规格的适配性(如玻璃尺寸需比窗框内沿小 5-8mm,避免挤压碎裂)。
2. 多部门图纸会审
组织设计、工艺、生产部门共同审核图纸,重点检查:
各部件尺寸是否存在矛盾(如侧板开孔位置与底板支撑梁是否冲突)。
材料折弯、焊接后的尺寸收缩量是否已计入(如钢板焊接后长度可能缩短 1-3mm)。
形成《尺寸确认单》,需三方签字后方可投产。
二、材料加工:精密下料与误差控制
1. 原材料预处理与选型
钢材类:
选用高精度冷轧钢板(厚度公差≤±0.1mm),下料前用校平机校准板材平整度(平面度≤1mm/m)。
不锈钢板切割时采用激光切割(精度 ±0.5mm),避免等离子切割产生的热变形(误差可达 ±2mm)。
型材类:
铝合金型材需从同一批次采购,测量其截面尺寸公差(如方管边长误差≤±0.3mm),杜绝混用不同批次材料。
2. 数控设备精准下料
关键工序:
底板、顶板切割:使用数控剪板机,设定尺寸公差 ±1mm,每切割 10 块板后用游标卡尺抽检 1 次。
型材折弯:采用数控折弯机,输入折弯角度(如 90°±0.5°)和补偿量(根据板材厚度预设 0.5-2mm),首件需用角度尺校验。
示例:钢板下料误差标准
部件类型 长度范围 允许误差 检测工具
侧板 ≤2000mm ±1mm 钢卷尺 + 塞尺
底板 2000-5000mm ±2mm 全站仪
门窗边框 ≤1000mm ±0.5mm 游标卡尺
3. 毛料二次加工修正
对切割后的板材进行边缘铣削,去除毛刺并修正尺寸(如板材对角线误差>2mm 时,需铣削短边至对称)。
型材焊接前进行预拼装,若发现尺寸超差(如框架对角线差>3mm),需用砂轮机打磨焊缝调整。
三、组装环节:定位工装与过程管控
1. 工装夹具标准化定位
底板定位:在工作台上铺设钢板工装,用定位销固定底板四角(误差≤0.5mm),确保长宽方向与基准线平行(偏差≤1mm/m)。
侧板组装:使用可调式角码工装固定侧板与底板夹角(90°±0.5°),每块侧板用水平仪校准垂直度(偏差≤2mm/m)。
2. 焊接与拼接误差控制
焊接工艺:
采用二氧化碳保护焊(电流 120-150A),分段焊接减少热变形(每段焊缝长 50-100mm,间隔冷却 30 秒)。
重要焊缝(如底板与侧板连接处)需做反变形处理(预设 1-2° 夹角),焊后用直角尺检测角度(误差≤1°)。
板材拼接:
两块板材对接时,错边量≤0.5mm(用塞尺检测),缝隙≤1mm,超过时需调整板材位置或补焊填充。
3. 模块化预组装校验
岗亭主体框架焊接完成后,进行整体预组装:
测量对角线差(如长 3m、宽 2m 的岗亭,对角线差应≤3mm),超差时用液压千斤顶校正。
安装门窗框,检查开关是否顺畅,框与墙体间隙≤3mm(用塞尺检测),否则需调整框体位置。
四、质检流程:多维度尺寸检测
1. 部件尺寸全检
对每个加工部件进行尺寸标注与实测:
底板:长宽尺寸 ±2mm,对角线差≤3mm,平面度≤2mm/m(用靠尺 + 塞尺检测)。
侧板:高度 ±1mm,垂直度≤2mm/m(用吊线锤检测),开孔位置误差≤1mm(如门锁孔中心距边缘尺寸)。
2. 成品三维尺寸扫描
使用激光三维扫描仪对组装后的岗亭进行整体扫描,生成点云数据与设计模型比对,重点标注:
整体长宽高误差(允许 ±5mm),顶部与底部平行度(偏差≤3mm/m)。
门窗洞口对角线差(≤2mm),窗台高度一致性(误差≤1mm)。
3. 模拟安装测试
在工厂内模拟现场安装环境:
将岗亭吊至预设基座上,检查四角支撑点高度差(≤2mm),否则需用垫片调整。
连接水电接口,测试门窗与周边结构的配合间隙(如卷帘门与门框间隙≤5mm)。
五、运输与安装:防变形保护措施
1. 固定包装设计
岗亭底部用角钢支架固定(支架间距≤1m),四周用木方支撑(接触部位垫橡胶垫),避免运输颠簸导致框架变形。
门窗玻璃用珍珠棉包裹,并用胶带固定在窗框上(防止晃动碰撞)。
2. 现场安装校准
基座施工时,用水平仪校准平面度(偏差≤2mm),预埋螺栓位置误差≤5mm(与岗亭底板螺孔对应)。
岗亭吊装到位后,用水平尺调整水平度(气泡偏移≤1 格),垂直度用吊线锤检测(偏差≤3mm/m),超差时用薄钢板垫片调整。